

So it that shouldn’t be the issue.Īnyone ever run into this? I may just give they guys at Inventables a call tomorrow to see what their thoughts are as well.Copyright (C) 2012-2022 by Autodesk, Inc.Ĭarbide 3D Grbl post processor configuration. I have also turned off any settings within Fusion 360 to leave stock. I did verify that I input the correct bit diameter of 1/8" in Fusion 360, and I also verified that my actual bit size is exactly 0.125". It almost appears that the bit size is off. The external dimensions of the piece were within 0.004" again, but the holes were 3.95", 2.968", and 1.975". As another test I cutout a test piece with a few large holes (4", 3", and 2"). I dialed in the stepper motors in the advanced setting of Easel so I was within 0.004" in the x and y directions.

When I cutout a few test pieces (varying in size from 4-10 inches in both the x and y directions) using g-code generated by Fusion 360 and imported by Easel, my outside dimensions were too large. Defining machine in Fusion 360 I am new and trying to define Shapeoko 5 pro in fusion.
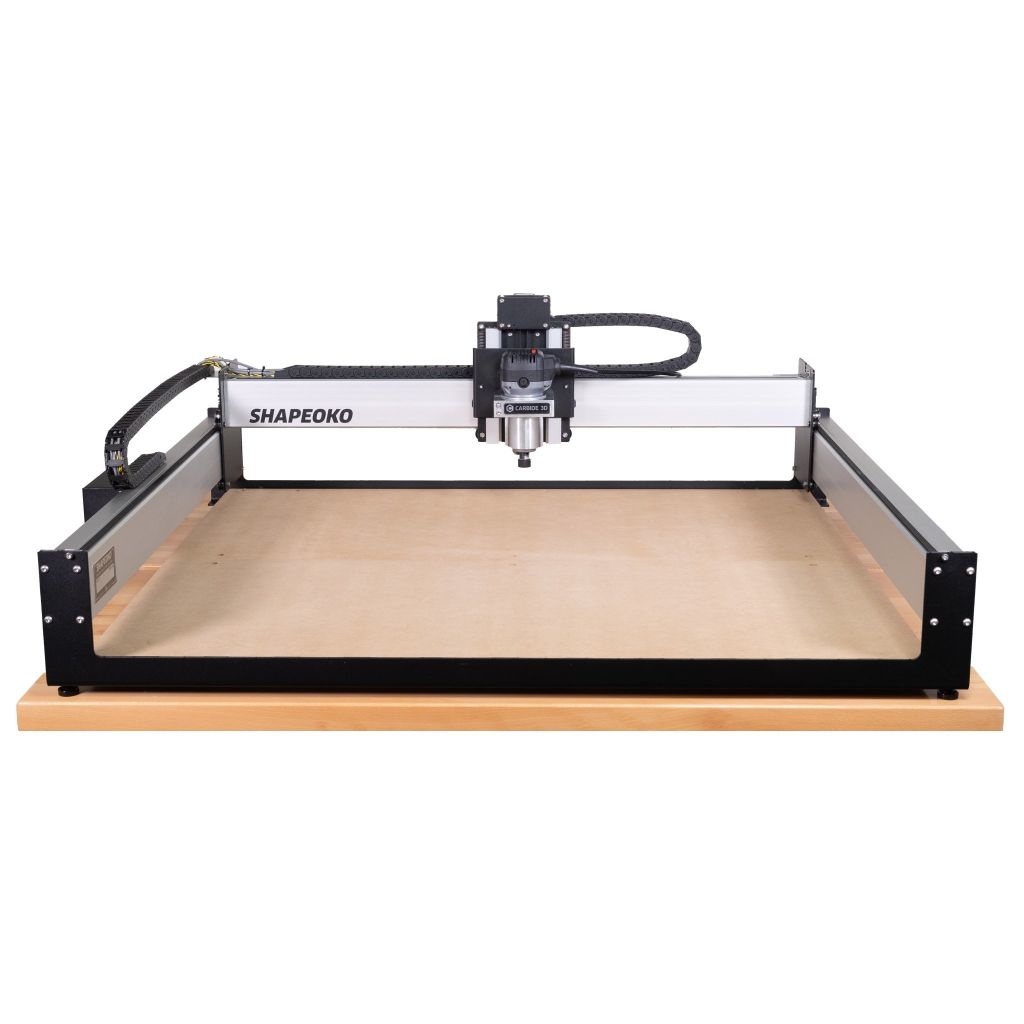
I’ve done a few more test cuts using hardboard with a 1/8" flat end mill pushed up into the collet as far as possible. I have attached my G-code file just to show what I have. I measured my end mill as well and it is exactly 1/8". I also matched the 1/8 flat end mill in Autodesk Fusion 360 with the 1/8 end mill in my router. I verified that I did not have Fusion 360 set up to leave material for rough cuts. I also did a few other shapes using different methods of machining (2D contour, 3D adaptive clearing) and got the same results, being 0.04" too large. After I cutout the part, the part was 1.74" x 3.04". The part I was trying to create was 1.7" x 3".
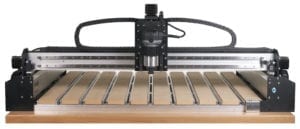
Since then I made a relatively simple piece in Autodesk Fusion 360.
